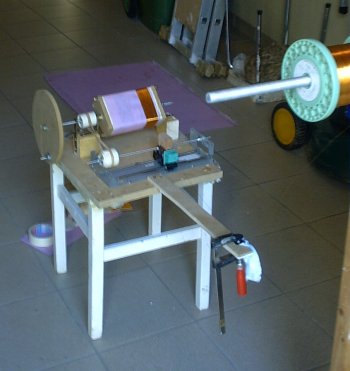 |
Inspired by Finn Hammer I intended to wind my own HV transformer almost one year ago.
But I just never found the time and motivation to really start winding this beast,
as 10000 turns on the secondary side just seemed way too many to be fun ;-)
However, recently my MOT stack went right up to hardware heaven and the failure mode was
that strange, that winding my own transformer became more of an option.
Obviously you don't want to hand wind this many turns, so I built a little winding jig with
leadscrew arrangement which made work a lot easier.
Honestly, I can't imagine what I would have done without the leadscrew, it makes the process so much
faster and easier. Here you can see how I made some test windings to calibrate the feed rate of the
leadsrew arrangement. The carrier for the leadscrew is made from parts from my old HP320 Inkjet
including the inc cartridge ;-)
As you can see: no electric motor here... just a little free exercise...
|
This is pretty much the same, just 38 layers and 10186 turns later. This should give me calculated 14600V out
( no special reason for that, I just ran out of the nice reddish paper ) with 230V in at 2,5KVA
continous or up to 5KVA for short runs. Now I will have to reassemble the core and find some oil
bath and ballast inductance for it. Hopefully it won't burn up during the first test ;-)
| 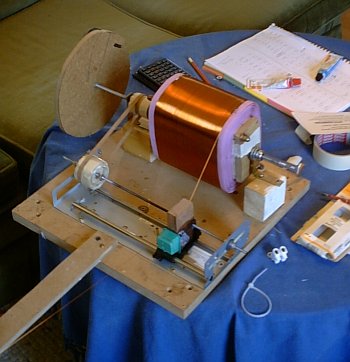 |
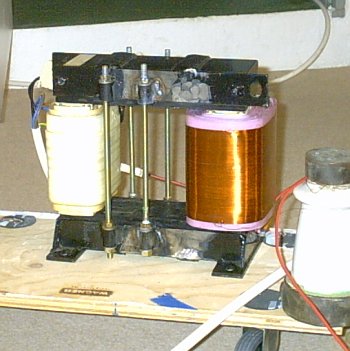 |
This shows the first test run of the transformer.
I shorted the secondary out and slowly increased the voltage fed to
the primary side until the primary current was 14Amps which is aproximately
the expected current here in TC or Jakobs ladder service.
This happened at 90V ( primary is 230V ), which gives an Uk of 39%.
I then connected a fairly close set jacobs ladder to the output and
raised the voltage up to 15V at which the transformer without ballast
draw up to 22A... pretty much. The secondary short circuit current was
almost 100mA, which seems pretty low... somwhere a substantional amount of
energy was lost. I even tried to move the coils closer together, with no
measurable difference to the normal configuration.
I let it run at 120V / 15A for two or three minutes and examined the core for heating.
Both coils were pretty cold, though the primary is only designed to take 10A.
But then I noticed, that the threaded bolts that hold the core together had become
too hot to touch. At the moment I have two, probably wrong, theories for that.
This was an 3 phase autotransformer, which means, that the major amount of
field was inside the coils, at least I suspect. Now the flux path goes all the way
around the core, probably seeing the bolts as shorted turns. Either magnetically,
which would raise the need for non-magnetic threaded rod, or electrically, which could
be solved by means of insulating washers. I did not have the time to try this, yet.
However, output voltage seems to be pretty high, as the jacobs ladder triggers with
much lower variac setting that with my MOT-Stack. Maybe there is still hope ;-)
|
Here is the final assembly of the transformer. The treaded steel rod was replaced by
brass threaded rod to avoid the problems with heating induced by eddy currents.
Additionally a terminal block was installed for the primary and ground connections.
The grey wire at the bottom connects from the central gounding point of the core,
where the inner end of the HV secondary in connected, to mains ground.
The transformer was tested with an air gapped mot core rewound with 160 turns stranded wire
for 20A in for 4600VA without PFC. Load was a jacobs ladder and test were dome at full input
voltage, though no oilbath was used. Everything held up well and visible performace was pretty god.
The problem, that the arc would not rise in the jacobs ladder was found in the jacobs ladder
itself, where dirt on the lower end of the wires made the gap in a place that narrow, that the arc
just would not leave this area.
I still have no really good idea for an impromptu oilbath. All plastic storage boxes I could
find were either to small or way too big. I want to keep the oil volume as low a possible for
reduced weight and less oilmess.
| 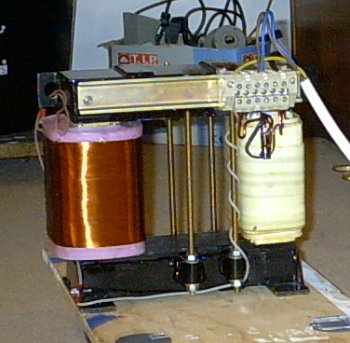 |
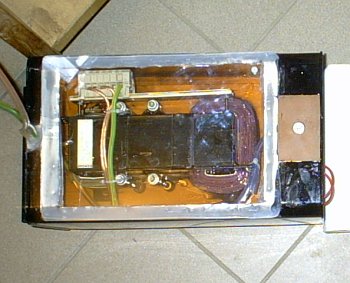 |
Because I needed this transformer up and running as quick as possible, I constructed
an impromptu oil bath from an empty paint can. The oil level is a little low as it only covers
the upper edge of the windings by 1mm but this was allthe oil I had at this time ( 20l)
The top cover is made from polycarbonate, so I can see when things should mess up inside the tank.
For now, I will try to raise the oil level by putting stuff like glass marbles in the tank... ;-)
|